In our first post on line balancing, we looked at the tasks that must be included in the line. In this second post of this series on line balancing, we look at the durations for the individual tasks. Of particular interest are different strategies on how to balance a line if the tasks have different durations for different products. A second consideration is if the equipment is already available or is still to be purchased (and hence can be customized more). The next post will look at more details of the losses (i.e., the OEE).
Lean Tools
Line Balancing Part 1 – Data Overview
Balancing the workload in a manufacturing system helps greatly in improving performance. Most importantly, it reduces unevenness (mura) due to different workloads. This in turn will reduce wasted waiting time (muda) for those with too little work, and overburden (muri) for those with too much. Additionally, I usually find it to be one of the easier aspects of lean manufacturing, since the new standard can simply be enforced through the layout of the machines. This post looks at data preparation, especially the customer takt and the list of tasks. It will be the first in a long series of posts on line balancing. The next post will look at the durations needed for the tasks.
Taiichi Ohno’s Chalk Circle
One of the famous teaching methods by Taiichi Ohno is the chalk circle. The method itself is simple. A circle is drawn on the shop floor near a point of interest. A disciple is put in the circle and told not to leave it until he is picked up again by the teacher.
In this post I will explain a bit about the chalk circle, how to use it for teaching, and how to use it for yourself.
How to Reduce Your Inventory
Reducing inventory is one of the goals of lean manufacturing. In my last post I described why we need inventory in the first place, and why too much inventory is bad for you. Now let’s look at how we can achieve a good inventory level. First, an important statement: Inventory is not a lever that you can pull. It is more the result of other good lean improvements. In fact, merely pulling this lever and reducing inventory will actually make things worse. To gain the true benefits of lower inventory, other measures have to be taken. In this post I would like to describe what happens if you simply reduce inventory, and how to do it to achieve a lower inventory without causing mayhem in the process.
Why Do We Have Inventory?
Inventory is expensive. Depending on your environment, inventory will cost you between 30% and 65% of its value. Toyota is known for (among other things) small inventories. Whereas Western companies often have weeks’ or even months’ worth of inventory, Toyota’s inventory is measured in hours.
It is no surprise that inventory reduction is high on the list for many companies. In fact, the term “lean” by itself implies lower inventories. But why do we have inventory in the first place? And why is (too much) inventory considered evil in lean manufacturing? In this post I would like to tell you the reasons why we have inventory in the first place, and why too much is bad. In my next post I will explain what happens if you simply reduce inventory, and discuss in more detail better approaches on how to reduce inventory.
How to Use an Andon – and How Not To
In my last post, All About Andon, I detailed how the mechanical side of an Andon signaling system works, including Andon cords, buttons, and boards. In the Western world, the mechanical side of an Andon system usually works pretty well. However, in most cases, the usage of the Andon is poor to nonexistent. Hence, in this post I tell you how to actually work with an Andon, and then I will give you a rant why companies so often mess it up!
All About Andon
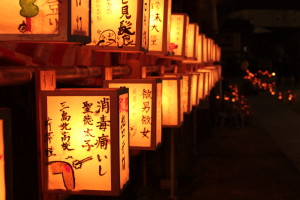
Andons are systems to alert operators and managers about current problems in manufacturing. The system automates the information flow in case of problems. An Andon system usually consists of the actual Andon, sometimes called an Andon board. Often, additional input and output devices are possible, the most famous being probably the Andon line, a cord that can be pulled to alert others about a problem. In a second post I will talk about How to Use an Andon – and How Not To.
Pay Attention to Details – Operator Training at Toyota and Scania

Often, implementing “lean” means management is picking the latest lean-related buzzword and telling their people to implement it. This is wrong on so many levels. For one, a lean project should always start with a problem, not a solution. On another level, good manufacturing is all about the nitty-gritty details. Both normal operations and improvement projects need a lot of attention to details. Unfortunately, this is frequently lacking in many companies. In this post I would like to show you the level of detail for operator training in some excellent companies.