Assembly of multiple parts into one bigger part is a common process in manufacturing. It is also the most challenging one for supply logistics. If there is only one part that gets milled, drilled, coated, formed, or other wise processed, logistics is much easier. But if you have dozens or hundreds of parts that have to come together in different variants, it becomes much more of a challenge. In this post I will look at the challenges of supplying material for assembly. In subsequent posts I will show ways to address these challenges.
Inventory
How to Deal With Long Delivery Times
Lean has a bunch of advanced but good tools for material delivery, like Just in Time, Just in Sequence, and Ship to Line. Using them is much easier on short distances and with short delivery times. Yet, sometimes you just don’t have the option of short delivery times. This blog post deals with the issues related to long lead times and delivery times.
How to Determine Your Lot Size – Part 3
This is the third and final post on lot sizes (Part 1 and Part 2). After considering all the factors of the processes and inventories (changeover time, batch size, customer order size, and container and shipment size), we now look at how to set up the information flow. This is especially important if we want to have different lot sizes in different sections of our value stream.
How to Determine Your Lot Size – Part 2
A good lot size has a significant impact on the performance of the system. In this second post, I look at the influence of the machine batch size on the lot size. I also briefly go into the lot sizes for the processing industry, and also administrative processes. In my next and last post I will look at how to manage different lot sizes in different parts of the value stream.
How to Determine Your Lot Size – Part 1
There are a few factors that can influence lot size: machine batch size, changeover time, size of the container, shipment sizes, and the size of your customers’ orders, which then are combined in the set up of the information flow. All of these factors can be influenced to move toward the true north of lot size one! Also, do not confuse the lot size with the number of parts per kanban. They are related but can be different. In this series of three posts, let me explain in more detail how the factors come together for you to determine the lot size of your processes.
Toyota’s and Denso’s Relentless Quest for Lot Size One
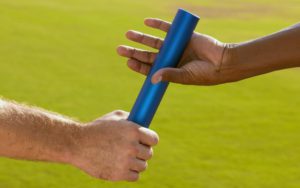
A famous step toward perfection in a lean production system is a lot size of one. However, few people realize what enormous effort and rigor Toyota applies to achieve this goal. During my visit to a Toyota plant and the APMS conference in Tokyo in 2015, I saw quite a few stunning examples of this quest. Let me show you …
Can you tell your Bottleneck from your Inventory?
On the shop floor it is common wisdom to find the bottleneck based on the inventory. If the buffer is full, the bottleneck is downstream. If the buffer is empty, the bottleneck is upstream. Is this true? My student Carolin Romeser and I spent quite some time verifying this, and found some interesting results. In general it is true, but … the devil is in the details.